Improving the efficiency of soft steam engines for robotics
-
skills: electromechanical assembly design • feedback control • data acquisition • data analysis • structure design • 2D thermo analysis • precise measurement (e.g., temperature, motion, force, power)
hardware: 3D printers (SLA, FDM) • laser cutter • shop tools
software: MATLAB • COMSOL • SolidWorks • Arduino • KeyShot
-
Creating robots from soft rubbers & plastics—i.e., “soft robots”—makes them conformable to odd shaped objects and surfaces, robust to compression and damage, and safer to operate around humans. The issue is that most soft robots remain tethered to lab benches (rather than mobile and autonomous) because of large compressed air tanks that are used to power and control their locomotion.
One solution to this issue is to use thermally-driven phase change—i.e., using heat to convert liquid to vapor, and using that volume change and pressure change to do work. While this is fine in concept, heat engines tend to be extremely lossy and no one in the literature was quantifying the efficiency of this approach. So, I undertook the (daunting) challenge of making a testing apparatus that uncovers what parameters (e.g., insulation, power input) have the greatest positive effect on the efficiency of soft heat engines.
-
I proposed that mechanical latching—i.e., the storage and then rapid release of elastic energy—might yield some efficiency improvement in thermally-driven soft robots. My collaborator Charles Xiao derived some thermodynamic theory that confirmed this hunch. He also confirmed that certain shapes of work cycles yield higher efficiency improvements (thanks Carnot). I then built the custom testing apparatus (see gallery below) to be able to test these theoretical findings.
The images and demo video really help understand what’s going on, but here it is in words as well: the testing apparatus is comprised of a soft pouch actuator containing a low boiling point fluid (Novec 7000) that is heated and cooled to perform measurable pressure-volume work on a hinge. A feedback-controlled voltage source supplies a quantifiable amount of energy to the pouch. That energy is converted into heat via a small piece of resistive fabric that is contact with the low-boiling point fluid. That fluid is then converted into vapor when sufficient heat has been delivered. Temperature, pressure, and angle (as a proxy for volume) are measured with high precision using temperature probes, a pressure sensor, and a potentiometer all in communication with a microcontroller (Arduino Mega 2560).
To test varying degrees of latching, the test setup uses a solenoid-actuated, feedback-controlled, 3D-printed latch to constrain the rotating hinge at certain angles (i.e., 0 and ~30 degs). To test the effect of cycle shape on efficiency, the test setup uses a combination of variable masses both on a loaded pulley and a stand fixed to the actuating hinge. The magnitude and position of masses on either of these mechanisms can be adjusted, producing a variety of different load shapes.
The outcome? We identified trends that confirmed theory and give soft robot designers guidelines on what parameters (e.g., latching, insulation, power input vs. power output) maximize the efficiency of their system. This work is the submission process for an academic journal.
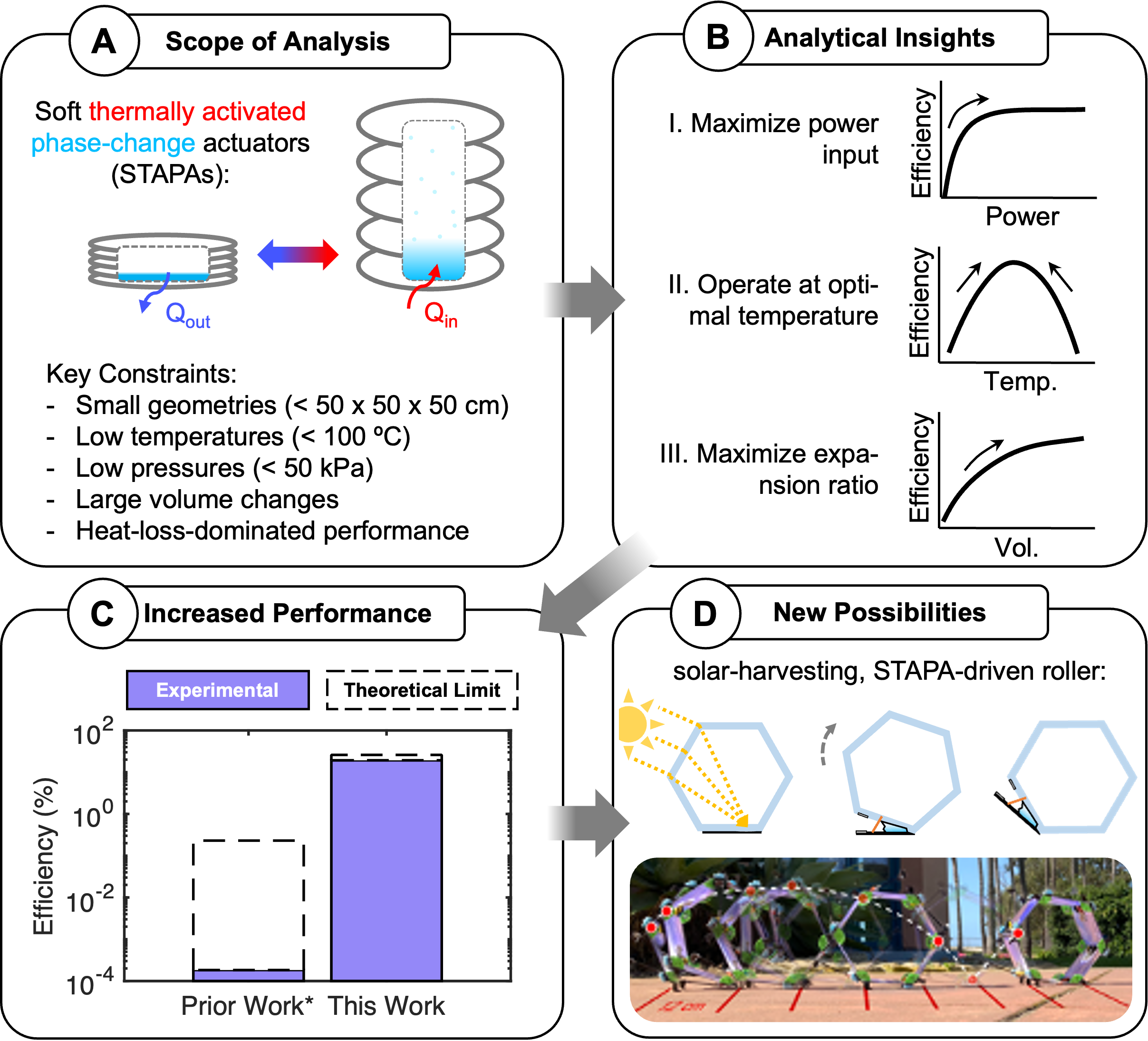
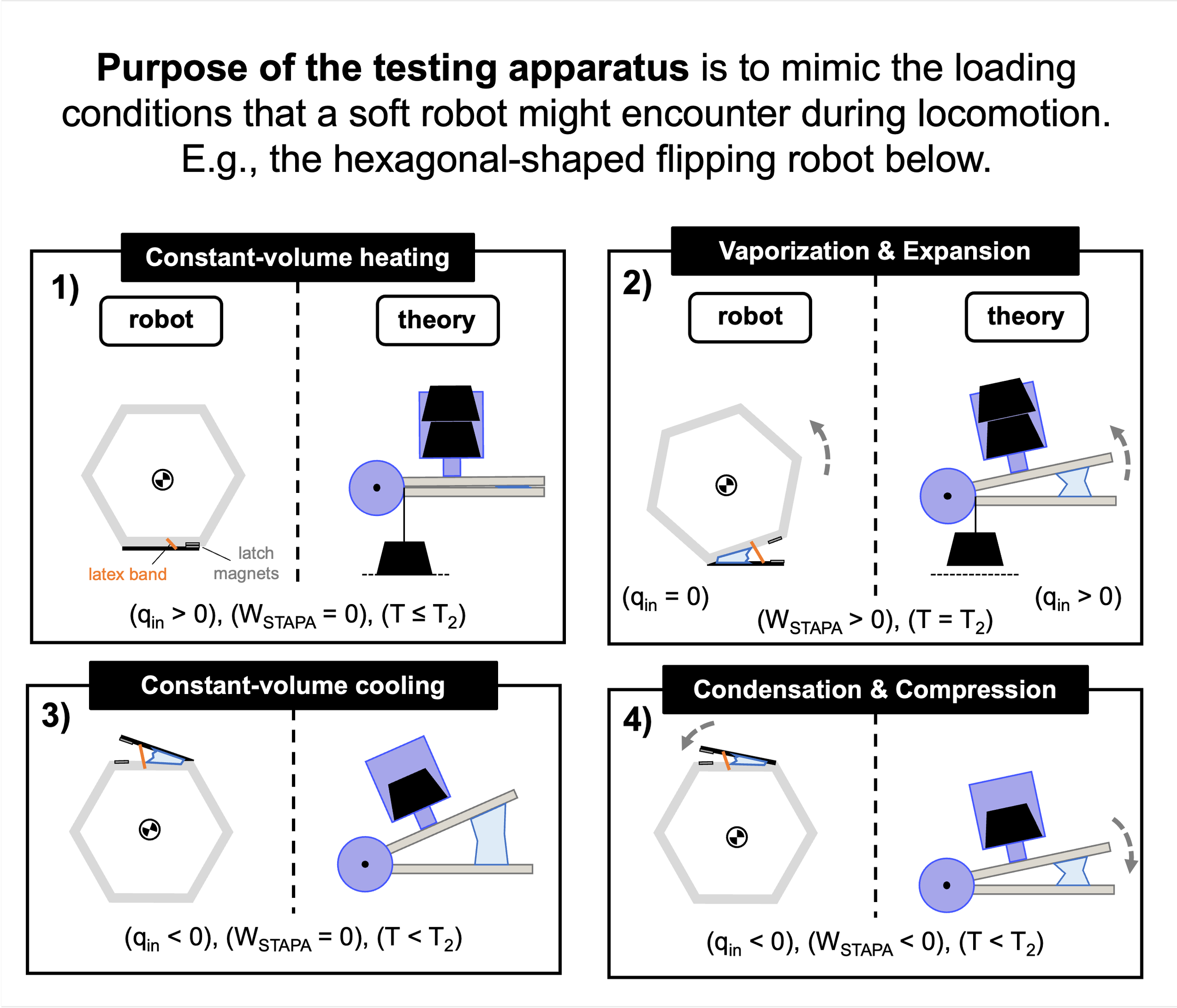
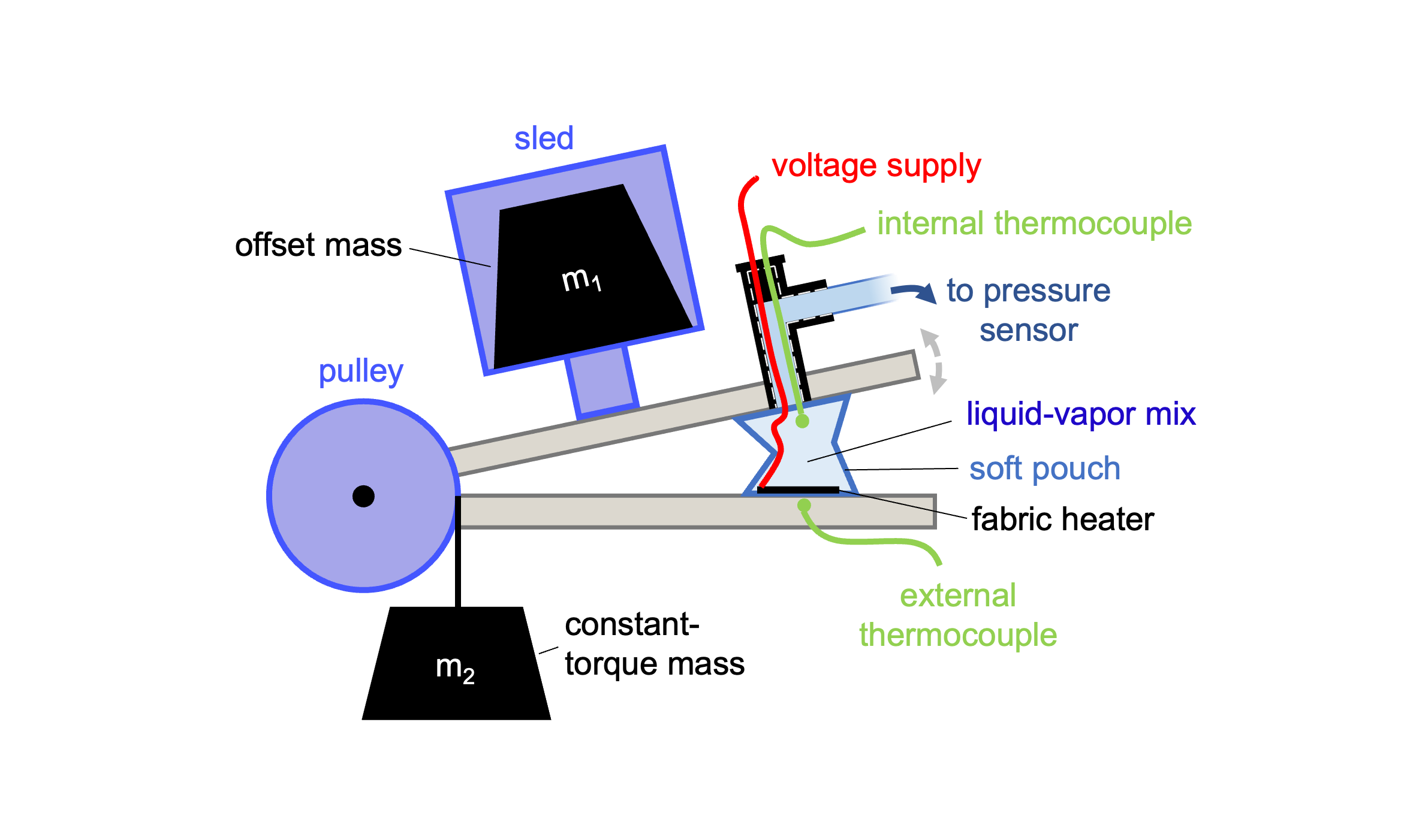
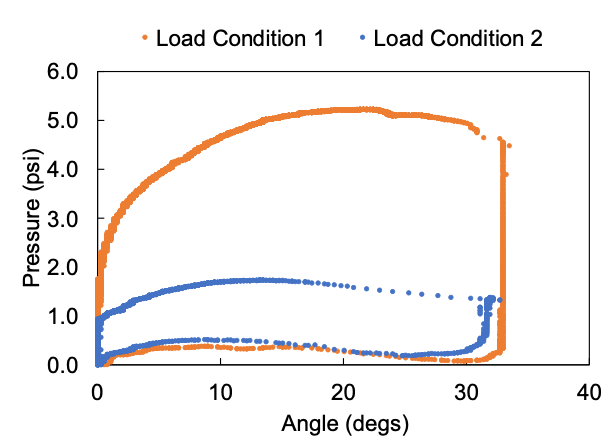
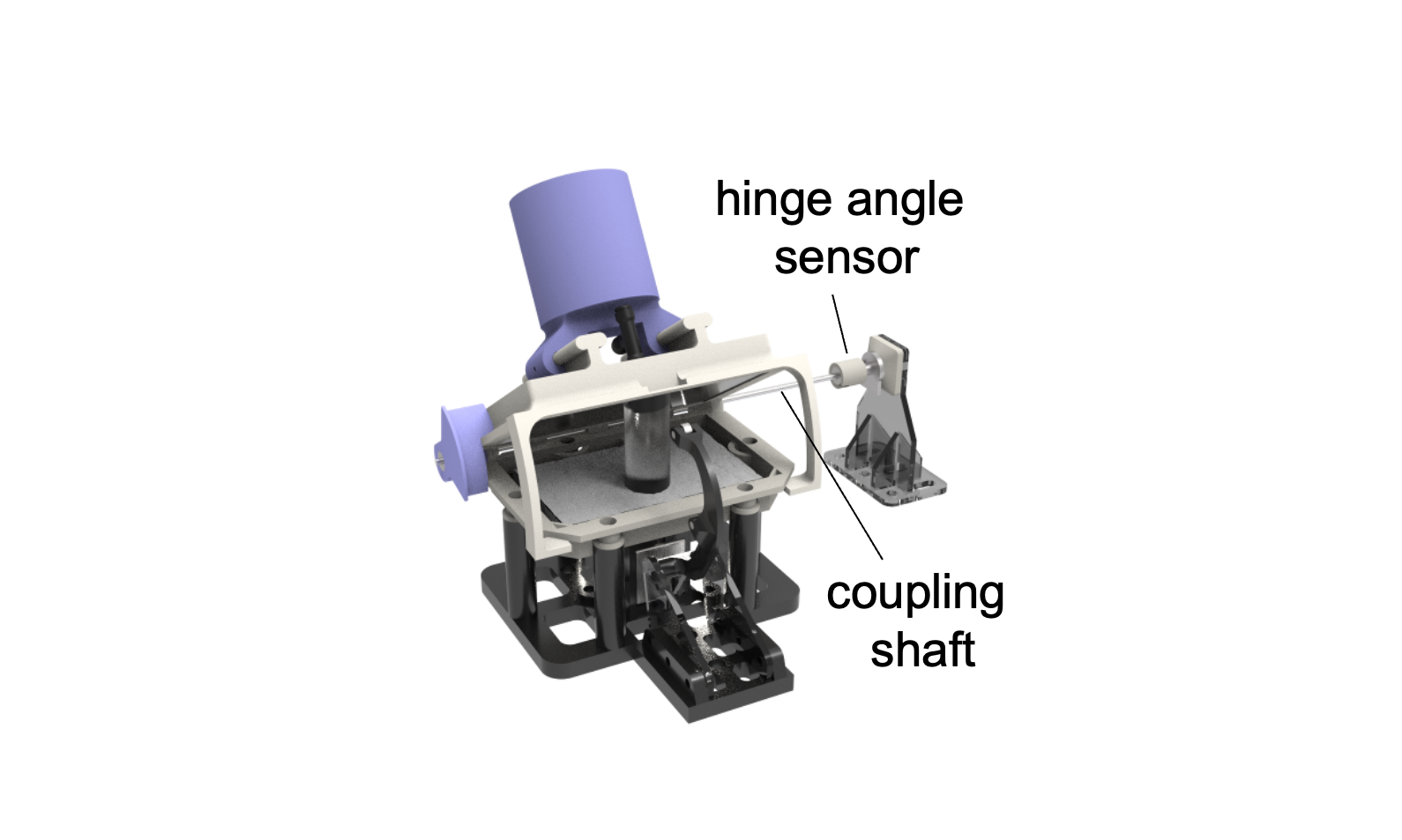
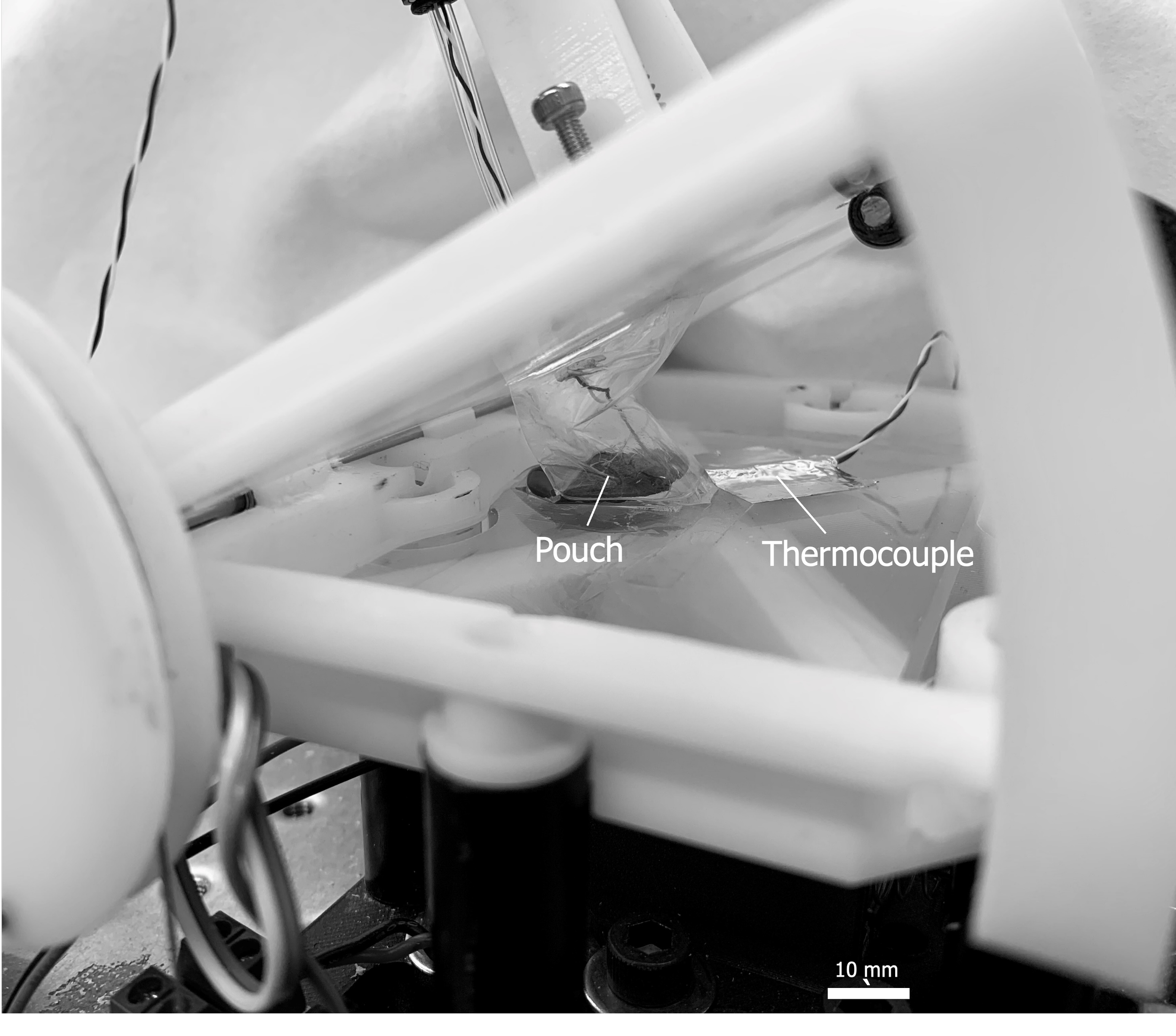


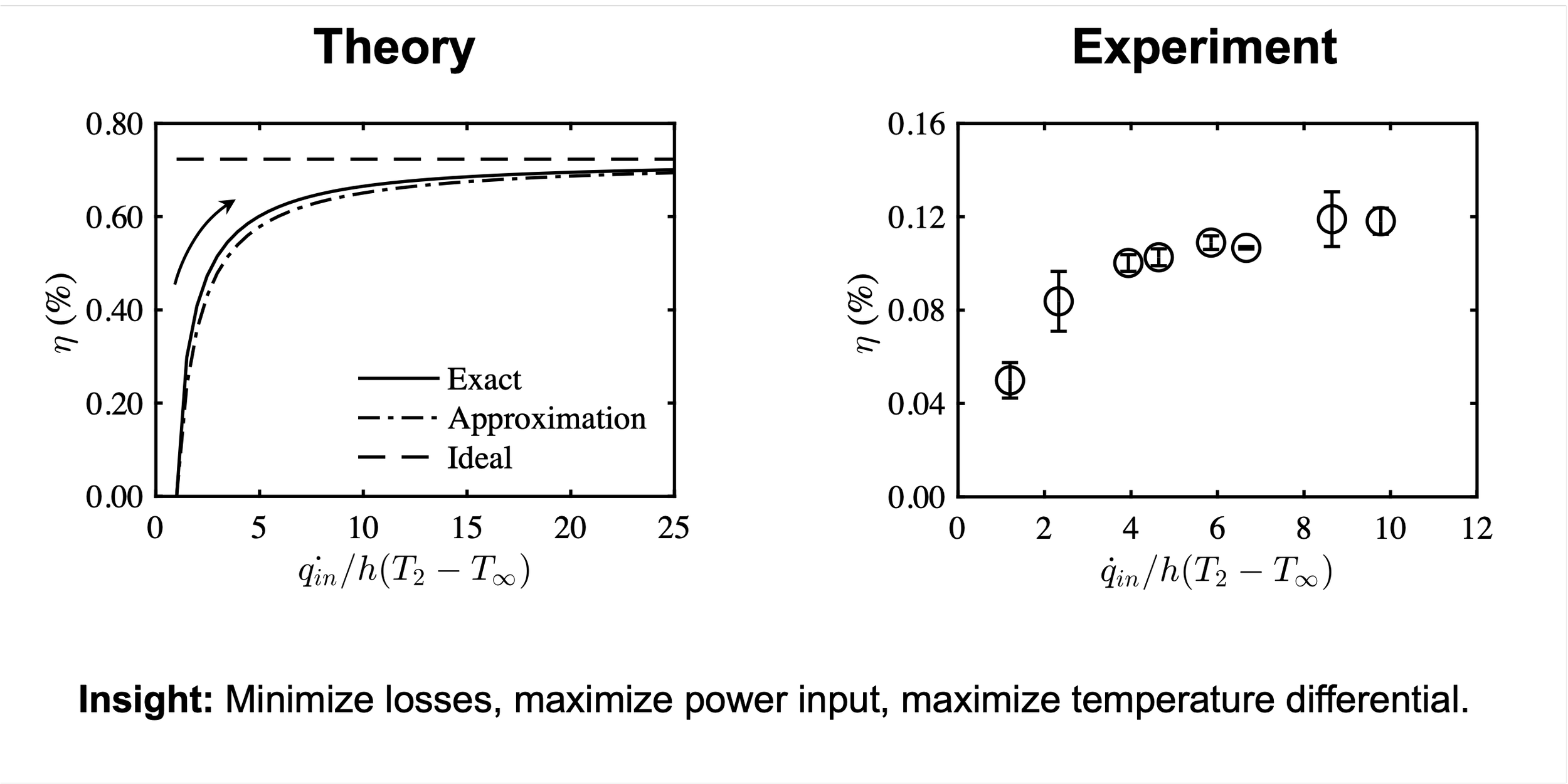
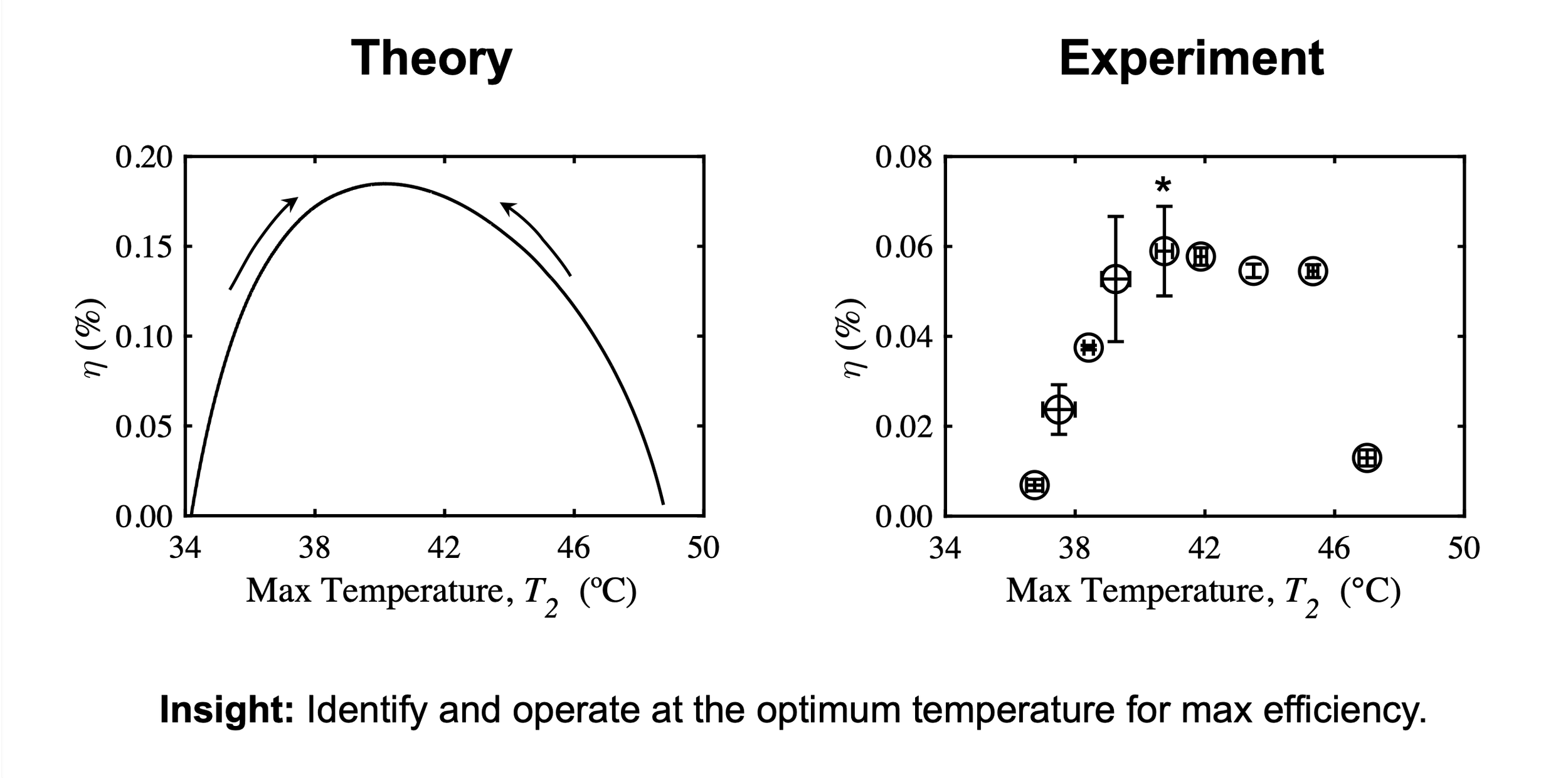
