Improving the efficiency of soft hot air engines for robotics
-
skills: meeting tigh deadlines • rapid prototyping • electromechanical assembly design • GD&T • feedback control • data acquisition • data analysis • structure design • 2D thermo analysis • precise measurement (e.g., temperature, motion, force, power)
hardware: 3D printers (SLA, FDM) • laser cutter • shop tools
software: MATLAB • SolidWorks • Arduino • KeyShot
-
Creating robots from soft rubbers & plastics—i.e., “soft robots”—makes them conformable to odd shaped objects and surfaces, robust to compression and damage, and safer to operate around humans. The issue is that most soft robots remain tethered to lab benches (rather than mobile and autonomous) because of large compressed air tanks that are used to power and control their locomotion.
A fellow lab-mate proposed that one solution to this issue is to use thermally-driven expansion of air. Hot air engines are something that Carnot proposed in his earliest descriptions of the heat engine, however, he was focused on air in rigid pistons. Because we were developing these hot engines in compliant pistons for locomoting soft robots, some reconsideration of the thermodynamic theory was required. In order to confirm that theory, a custom testing apparatus for measuring efficiency was required… which is where I came in. 😅
-
This work was part of a three-week sprint to see if we could prototype a soft hot air engine for a robotics conference (IROS).
If you've ever taken a thermodynamics class you know that converting heat into work can be a highly inefficient process and that cycle design (e.g., getting as close to the Carnot cycle as possible) is the only route to efficiency. Despite this, most people designing soft robots were using heat engines (either phase change or air-based) and heeding none of the thermodynamic theory. Bucking this trend, my collaborator Charles Xiao developed some theory showing that emulating an Otto-like work cycle could yield some efficiency benefit.
To confirm his hunch, Charles and I built the necessary experimental setup. Charles built a soft piston comprised of a thin plastic film wrapped around two rigid plastic dishes. A small wire inside of the piston serves as a Joule heater--delivering quantifiable amounts of heat energy to the encapsulated air.
I developed the surrounding sensors and loading apparatus. Energy and power into the system are measured via a digital power meter. Temperature of the air inside of the piston is measured in two places using K-type thermocouples. The position of the piston head (serving as a proxy for volume) are measured both using a Hall effect sensor (to detect non-zero volume change) and a potentiometer (to approximate volume). Finally, masses are positioned and added/removed from the rotating shaft by hand in order to program specific load cycle shapes.
The outcome? We demonstrated that you can improve efficiency 1,130% going from a conventional/common rectangular-shaped work cycle to an uncommon downward-sloping parallelogram-shaped cycle. You can read more about this in the write-up on arXiv.


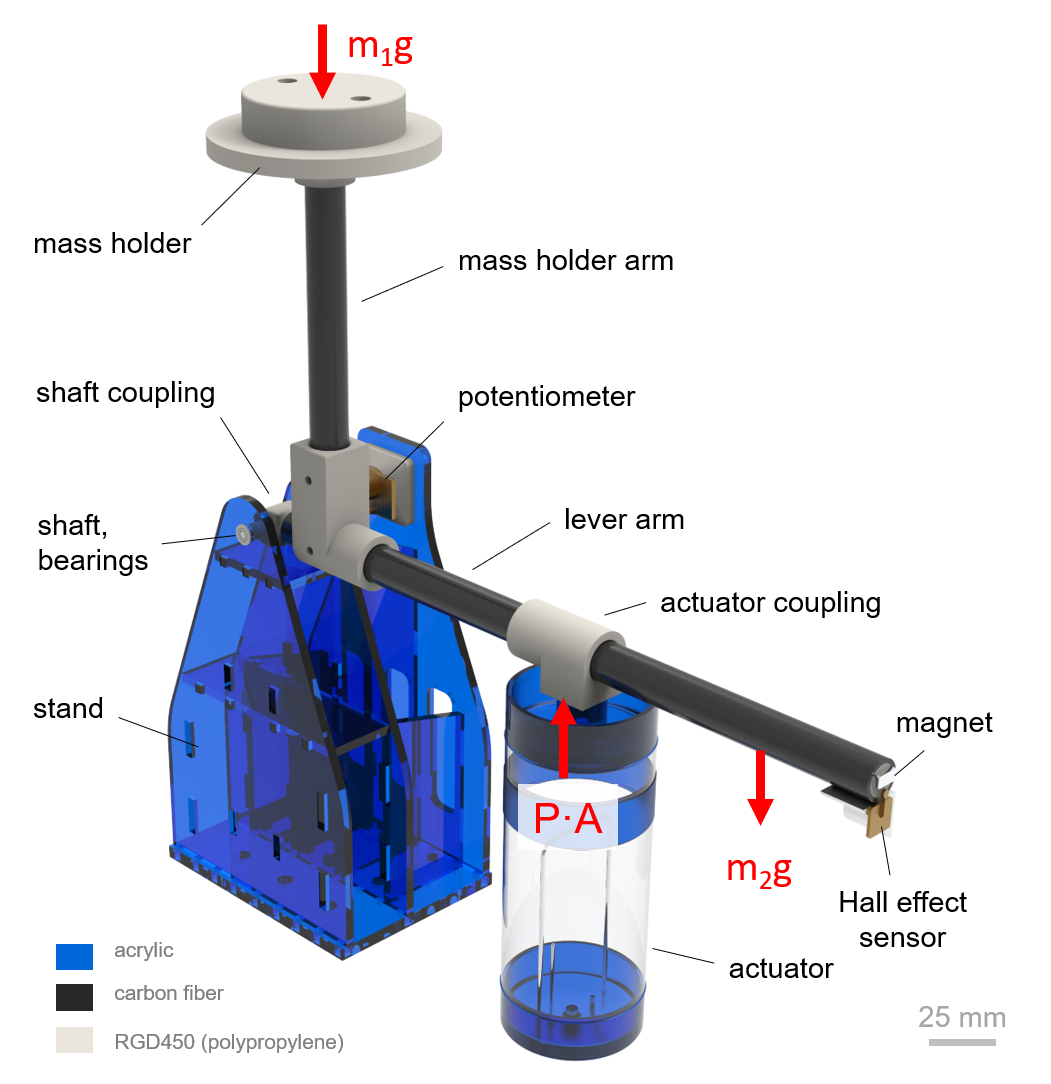
