Oil & gas manifold design improvement
-
skills: fluid dynamics principles • computational fluid dynamics • data analysis • technical communication • design for manufacture • cost reduction
software: SolidWorks • SolidWorks Flow Simulation
hardware: n/a - the client fabricated the design
-
Hydraulic fracturing (i.e., fracking) uses 18-20 pumps per fleet. These pumps comprise a power end and a fluid end. The fluid end is the body situated inside of a frack pump that interfaces directly with the fracking fluid. It allows for the passage of high-pressure fluid into the fracking well. The average lifespan of a stainless steel fluid end is an appalling 750-1800 hours (at most, 75 days) due to constant high-pressure operation and the harsh and abrasive fluids required for fracking. This lifespan of a fluid end is the result of several factors: fluid choice, the quality of frack sand pumped through it, and the pressure conditions present inside of the channels.
During my internship at KCF technologies, our team was approached by a client who had noticed serious deep pits (where material had been removed) on the valves inside of the fluid ends (see image in gallery), potentially indicative of cavitation. Cavitation occurs when the static pressure of a liquid drops below the liquids vapor pressure, leading to small destructive bubbles of vapor that can collapse and damage machinery. Eager to apply some of the fluid dynamics simulation knowledge I had just learned in a workshop, I took it upon myself to come up with a few designs.
-
Cavitation is a highly localized phenomenon that’s hard to capture in computer fluid dynamics (CFD) analysis packages like the one I was using without high-resolution meshes and significant computational power. Instead, I focused on the correlation that the client noticed between high pressure spikes and drops (see chart in gallery) and significant damage on their components.
Using customer-specified parameters (e.g., pumping pattern), I modeled the pressure, speed, and flow rate of fluid in their current manifold and proposed a new manifold design. This manifold, which I called the “Mammoth Manifold,” had lower drops in pressure, near-constant fluid velocity through each port, fit within the ergonomic constraints of the fluid end, and served as potential solution to their "$10M/yr problem." T
The outcome? I showed my findings to company leadership (CEO, CTO), got enthusiastic endorsement, and then took the design to the client. The design was then constructed by welders and used on several fleets after my time at KCF (see gallery).

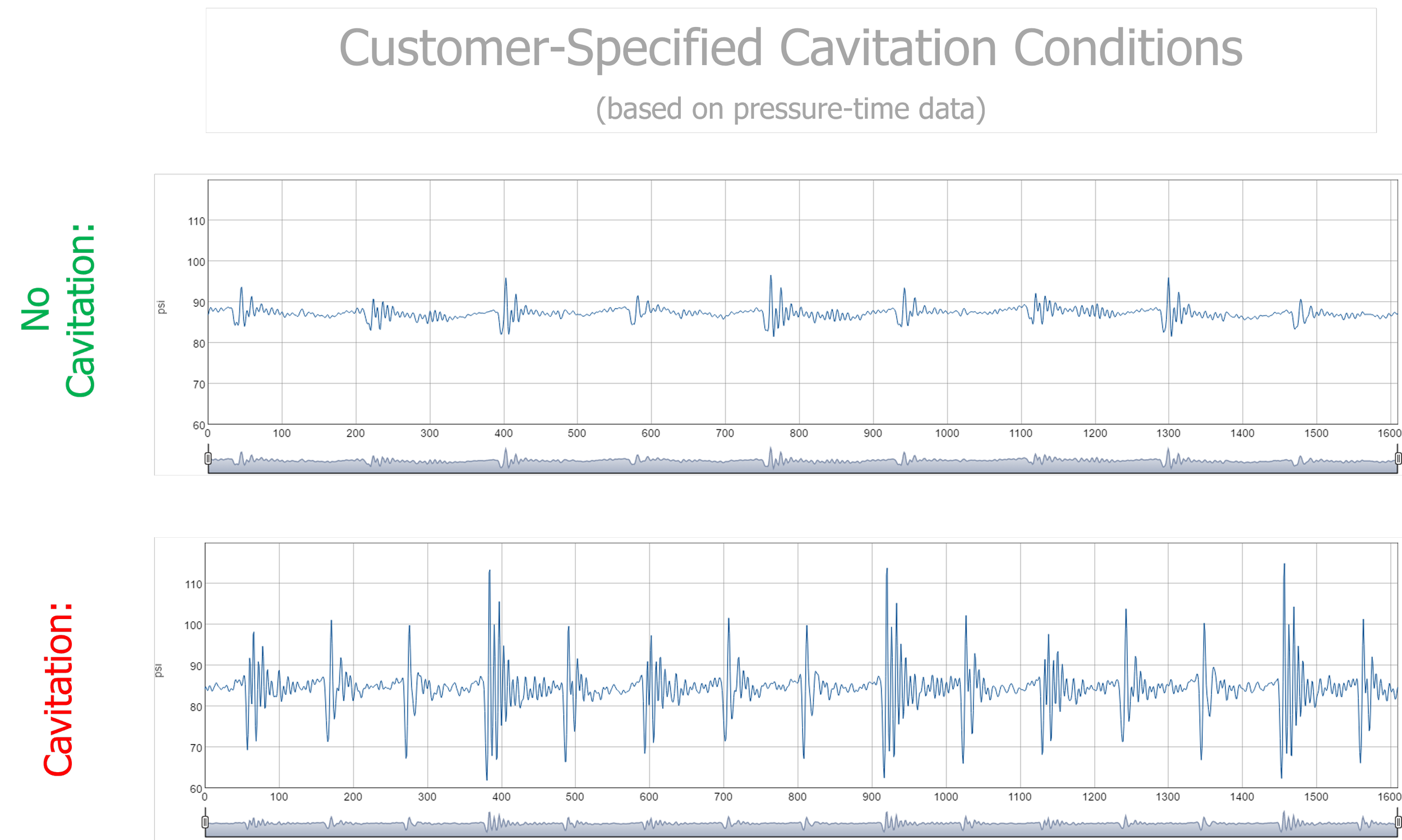
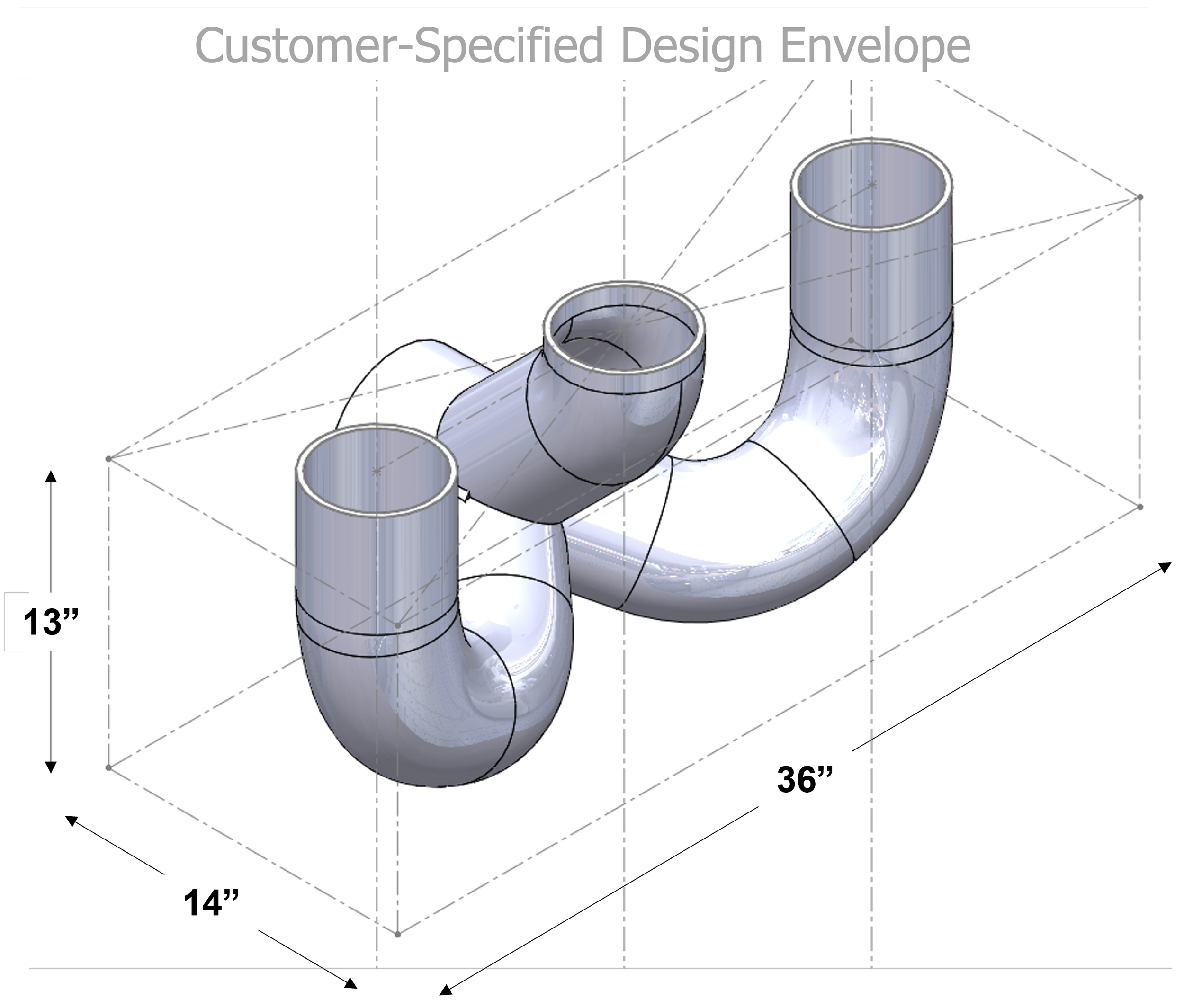
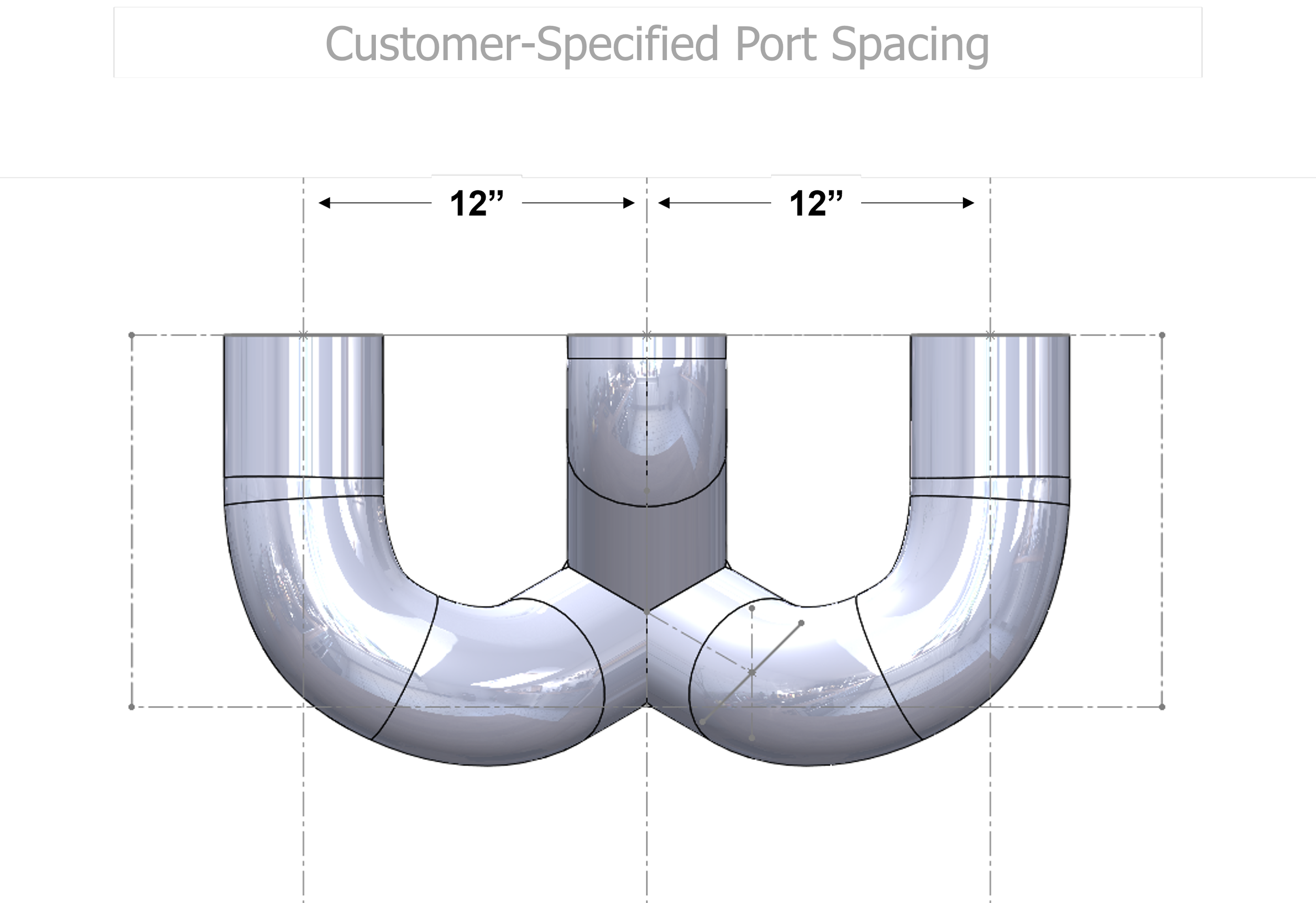
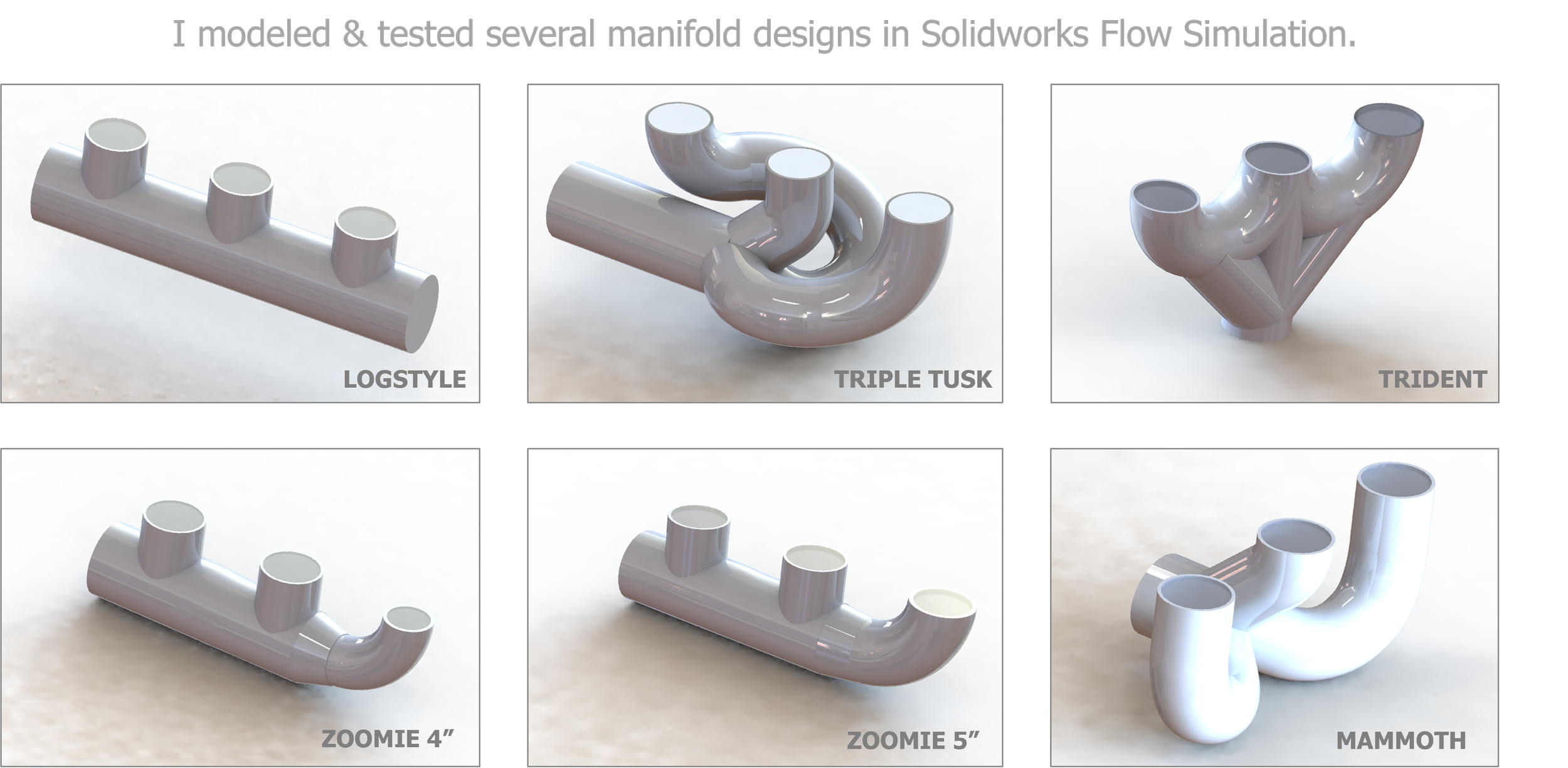
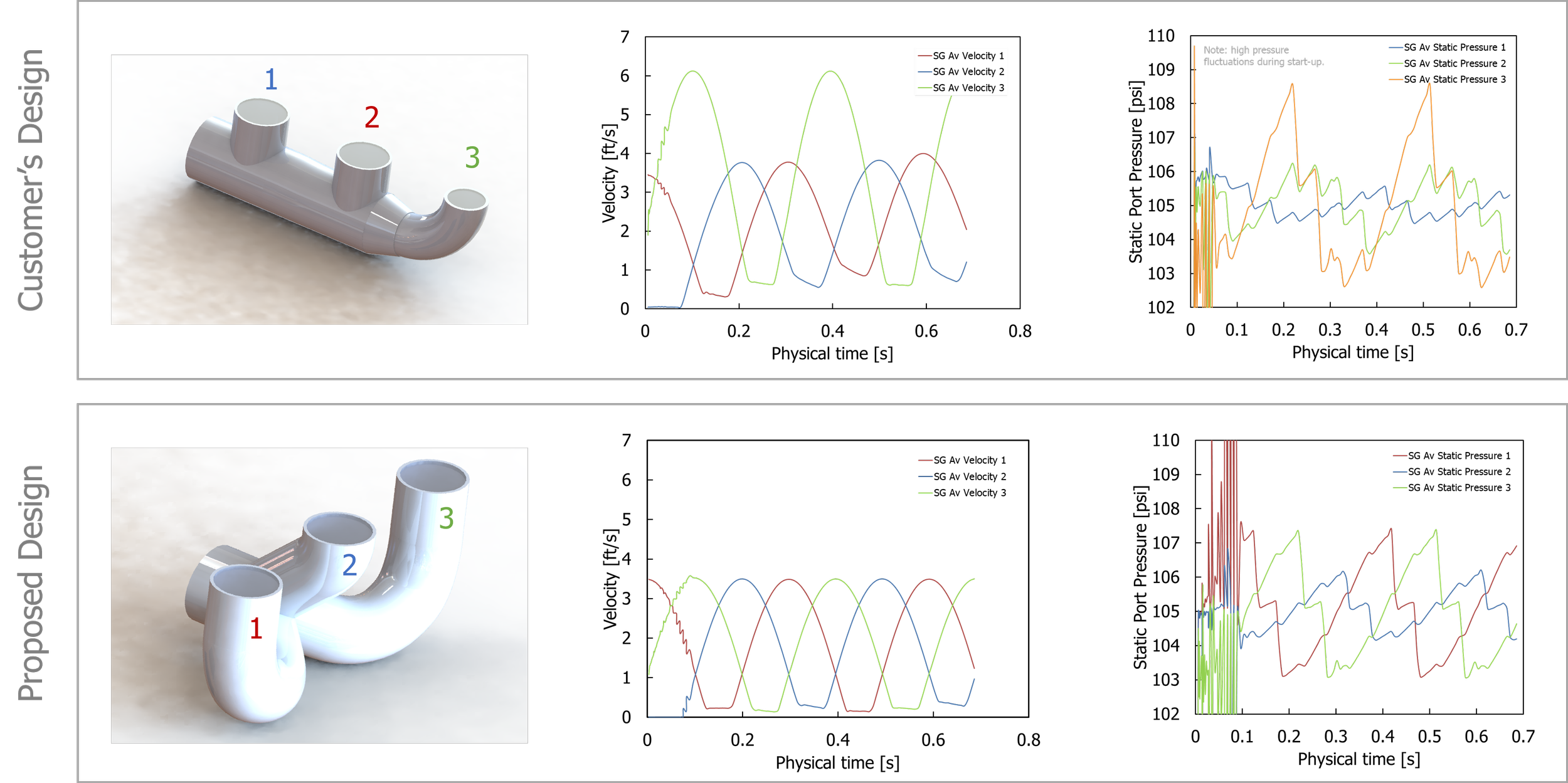

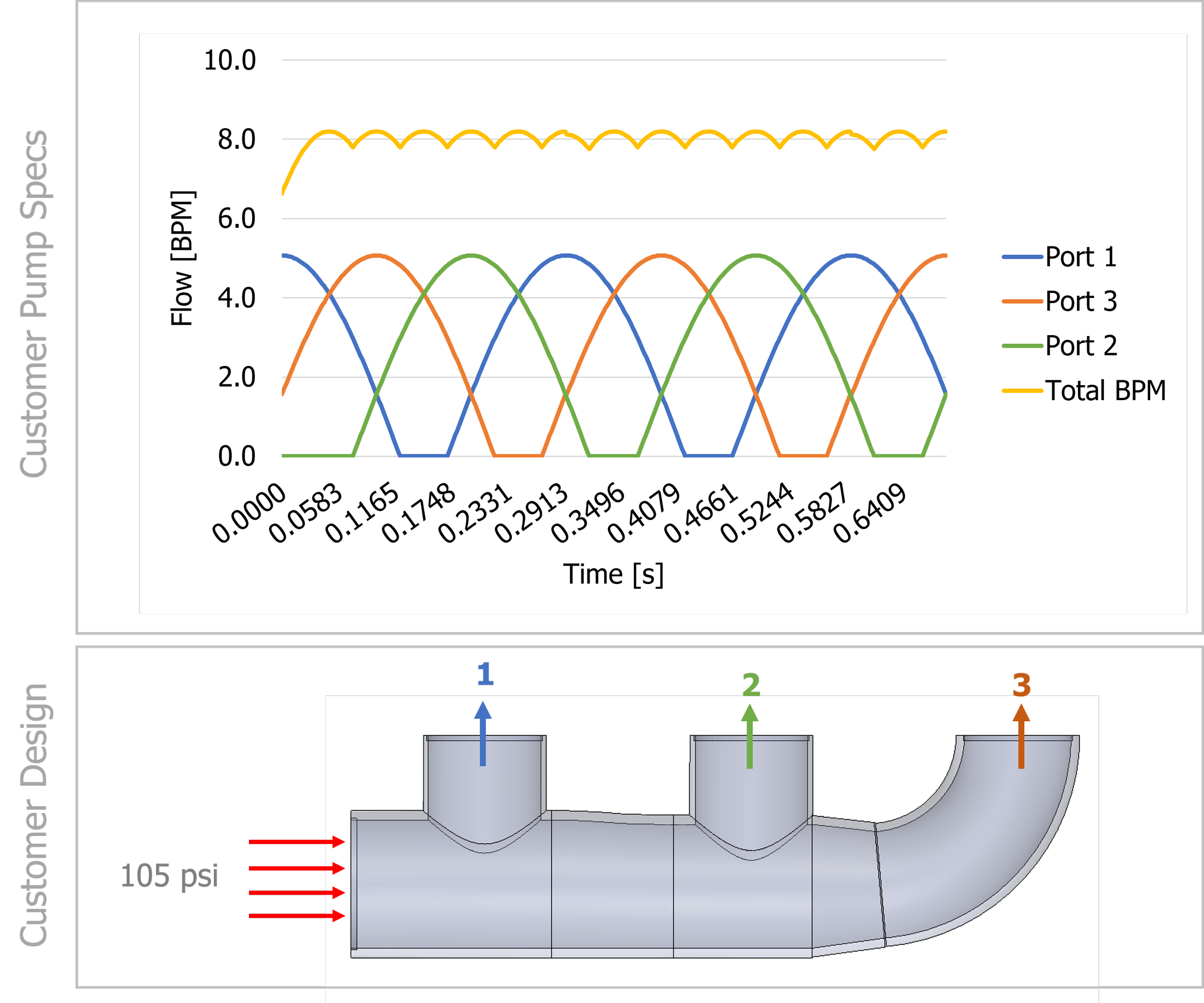