Cooling system for a formula racecar
-
skills: leadership • thermodynamics • molding & casting • composite fabrication • thermodynamics • rapid prototyping • teamwork
hardware: lathes • end mills • sanders • drills • general shop equipment
software: Solidworks • Excel
-
In my first two years at Penn State, I was heavily involved in the formula society of automotive engineers (FSAE) and took responsibility for our cooling system. FSAE is a student design competition organized by SAE International. Each student team designs, builds and tests a prototype based on a series of rules, whose purpose is both ensuring on-track safety (the cars are driven by the students themselves) and promoting clever problem solving.
To be successful in the demanding and competitive annual racing competition, I took responsibility for keeping our 2010 Yamaha YZF-R6 engine cool even on a blistering day in Michigan. A high-performance cooling system needed to be designed that met weight, packaging, price, and power constraints set both internally by our team and externally by the judges of the competition.
-
I designed a heat exchanger using the NTU Method and outsourced the fabrication to a local manufacturer. Heat from the engine is transferred to coolant that flows through the engine block and eventually to the heat exchanger (basically an array of aluminum channels). That heat exchanger then transfers the heat to surrounding air.
To enhance this exchange, I designed, molded, and fabricated a carbon fiber shroud that pulled cool air through the heat exchanger and jetted it out towards the back of the car (see gallery). Lastly, I spec’d out a water pump that drew minimal electrical energy away from the car battery while pumping sufficient coolant through the engine block to effectively cool it based on my NTU method calculations.
The outcome? We didn’t place in the 2014 season, but our cooling system performed without fail throughout the competition, most notably during endurance events where some cars overheated and failed.
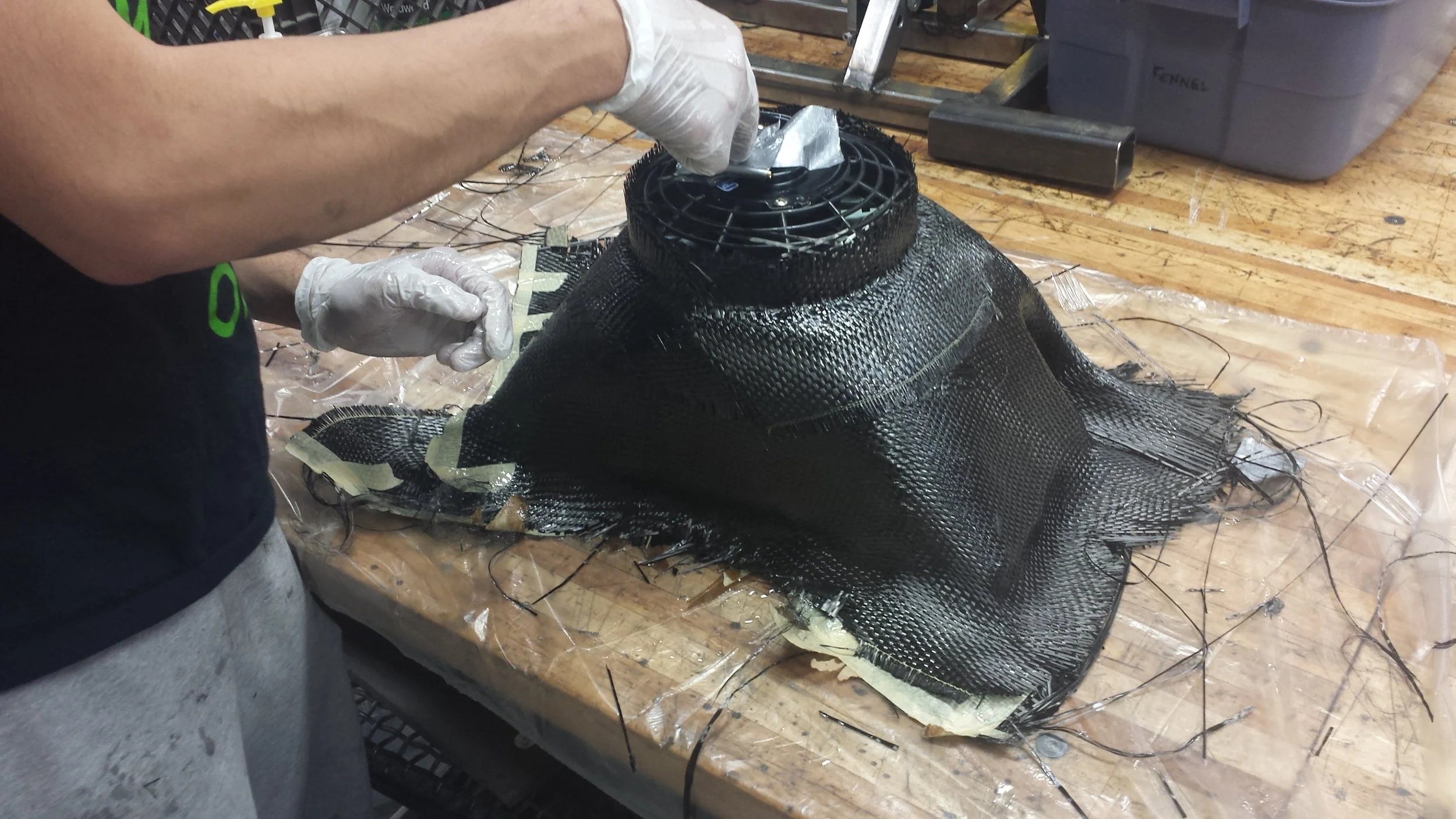