Design & fabrication of a soft solar-powered robot
-
skills: open loop feedback control • compliant mechanism design • structure design • optics design • thermodynamic analysis • extreme perseverance & patience 😮💨
hardware: 3D printer (FDM) • laser cutter • shop tools
software: MATLAB • SolidWorks
-
A core challenge for the field of soft robotics is untethering fluidically actuated robots from unwieldy power sources to increase their mobility and functionality. One potential solution explored in the literature is the soft heat engine, which uses wirelessly activated, thermally-driven liquid-to-vapor phase change processes to do work. Phase change processes are an attractive means of untethering from pneumatic pumps because they enable large strokes and impressive forces.
During my PhD at UCSB, I teamed up with thermodynamic theoreticians to analyze dominant sources of energy loss in soft thermally actuated phase change actuators. We identified three applicable strategies for minimizing losses, I experimentally confirmed the validity of these insights (using the testing setup elsewhere in my portfolio), and I then applied them in the design, construction, and operation of a compliant roller capable of locomotion using only sunlight.
-
To be honest, it all began with a silly flipping robot.
I was wrapping up a project about photoswitches. We were characterizing a molecule that could absorb light, generate a bunch of heat, and then turn clear (and not absorb a bunch of heat). I got curious if we could leverage this for self-regulating phase-change-based actuation (like a steam engine that turns on and off despite constant input of energy).
I started with a two-sided robot (that looked like it was standing and then faceplanting every few minutes). That robot eventually (with a lot of thermodynamic analysis and carful thought) turned into a six-sided robot that used sunlight to locomote.
How does it work? For a given side, actuation is made possible as sunlight is collected and concentrated through asymmetrical Fresnel lenses onto an adjacent pouch, which is nestled between the robot leg and its body. The pouch contains an absorber which is in contact with a low-boiling point fluid (it boils ~93 °F). As light is absorbed, heat is generated, the fluid is vaporized, and the phase change generates increasing pressure until sufficient pressure is generated to overcome the force of a magnetic latch and flip the roller about a cloth hinge. If you’re confused, the images in the gallery (below) help a ton.
All sides are identical in construction. A fiberglass leg enables force transduction from the pouch. Magnets adhered to the leg create a latching mechanism that enforces a threshold pressure for actuation. Latex bands serve as a restoring load during the compression step of the cycle. Polystyrene foam minimizes heat losses to the body. Dynamic hinges offer stiffness during regular robot operation but can deform bi-directionally under loads that exceed the roller’s weight.
Engineering? Plenty. A lot of hands-on engineering and rapid prototyping went into getting the robot body design just right. The design and fabrication of the little polyethylene pouches was an exercise in origami. Designing the body—both its structure and weight—was a long and iterative structural design exercise to create a stiff structure (for force transduction) that could be compressed (for robustness) without damage. Designing the latching mechanism involved was terrible fun and required free body diagrams of reactive forces between an inflating pouch trying to press against a rotating hinge that was held shut by magnets and the weight of the robot. Overall, this project flexed a lot of my engineering fundamentals and I had a ton of fun (in between long periods of frustration) doing it.
The outcome? A slightly less silly flipping robot. You can watch a video of me squishing it while it flips around here. Images in the gallery below.
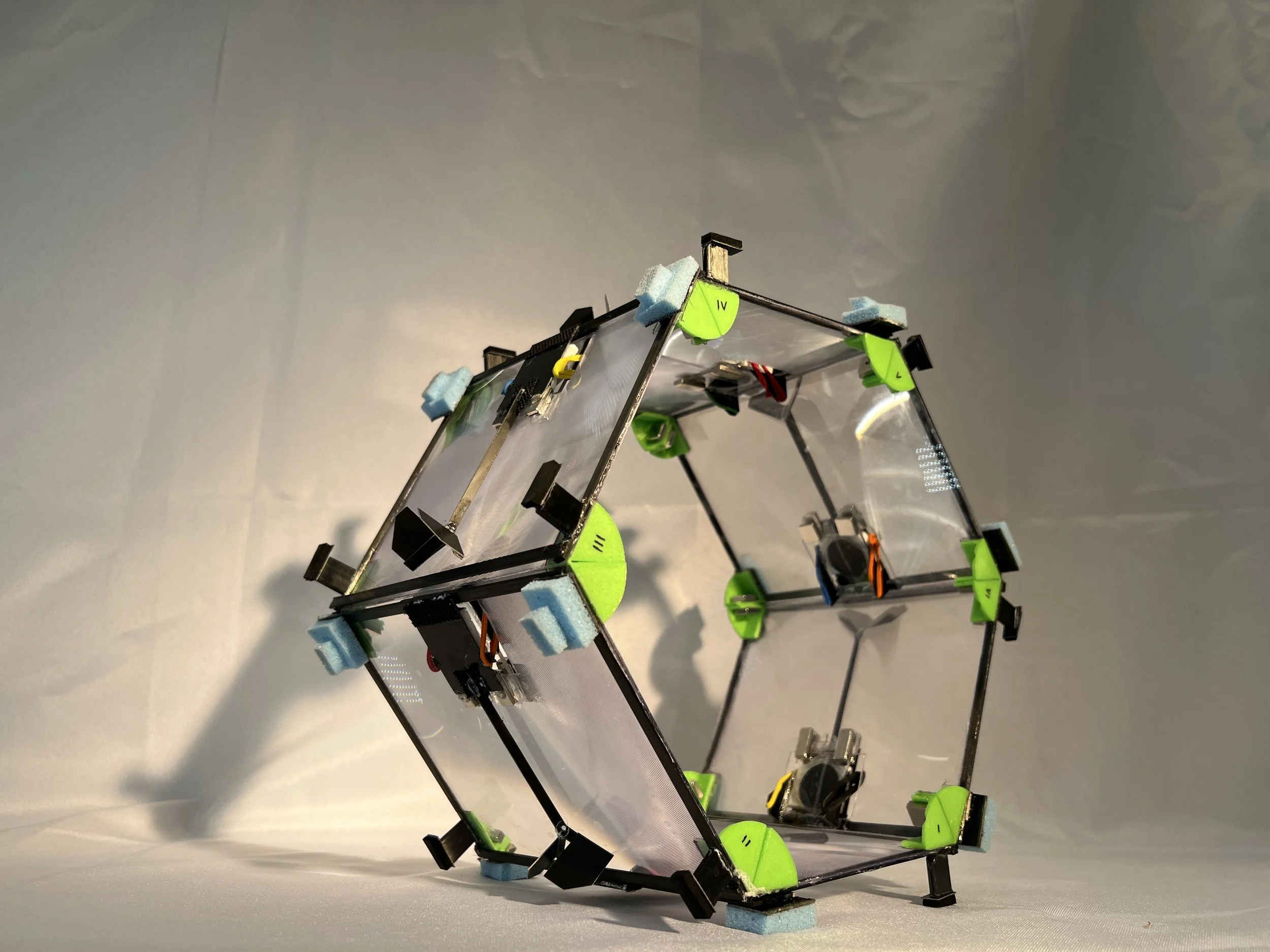
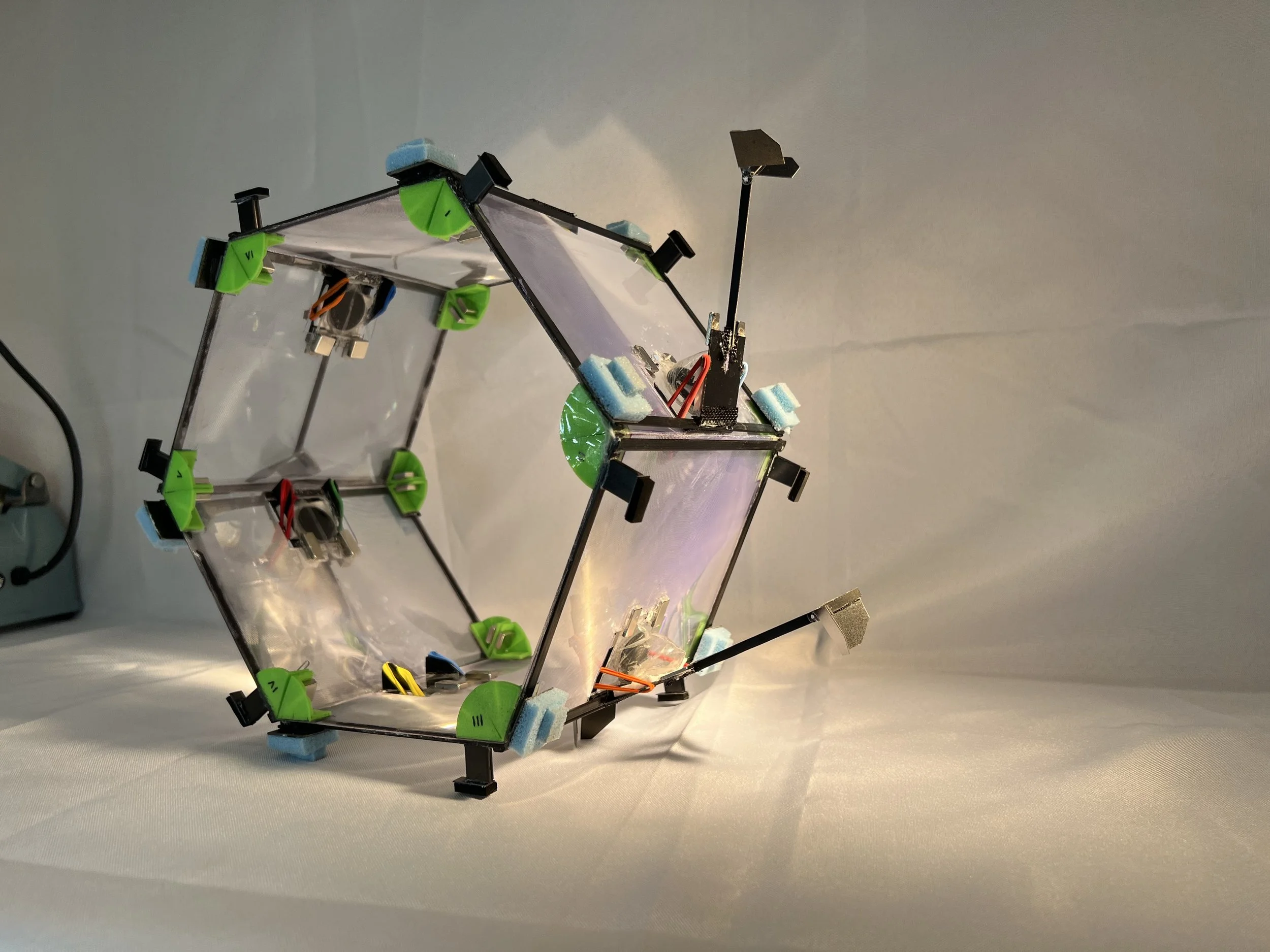
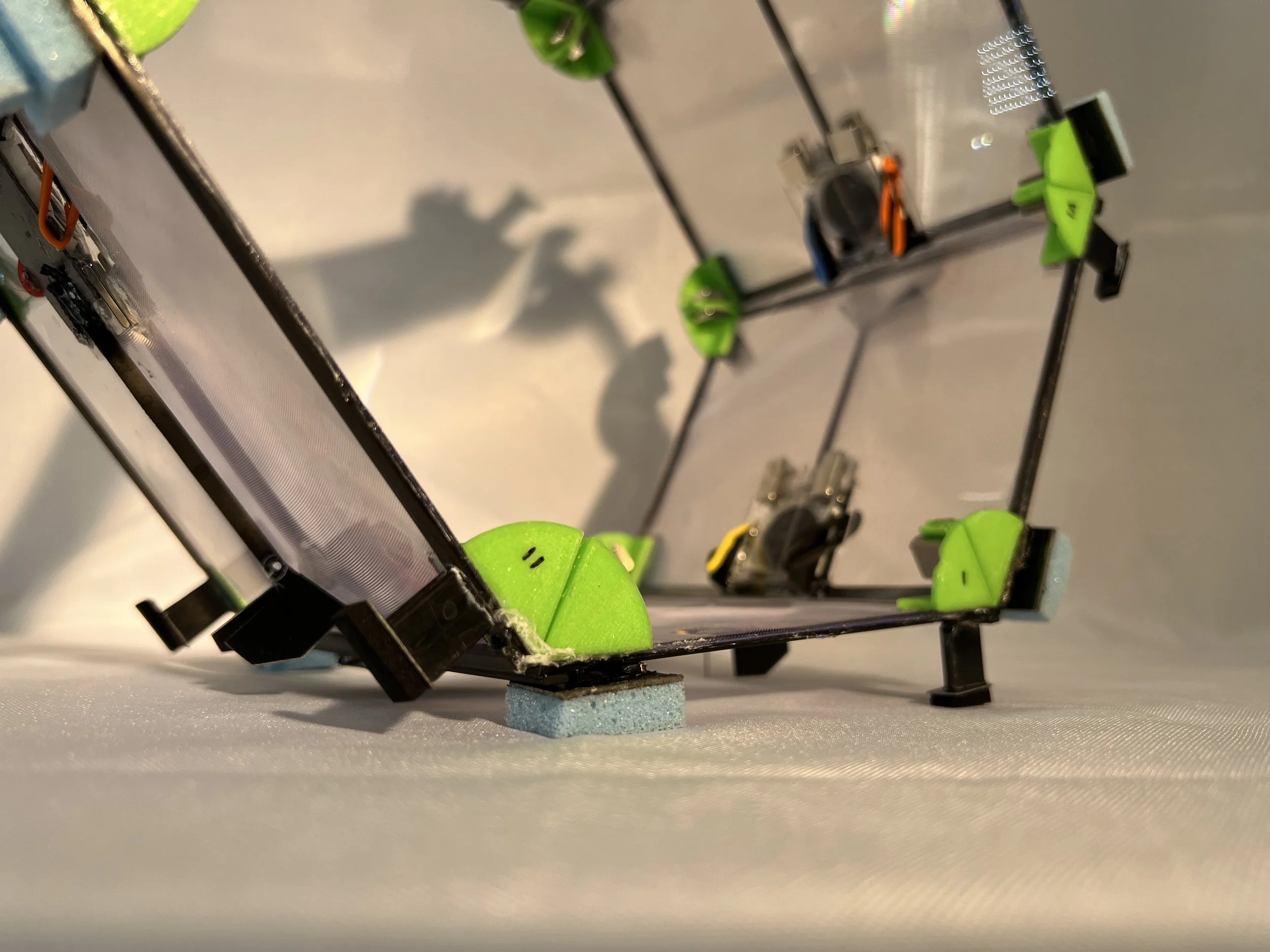
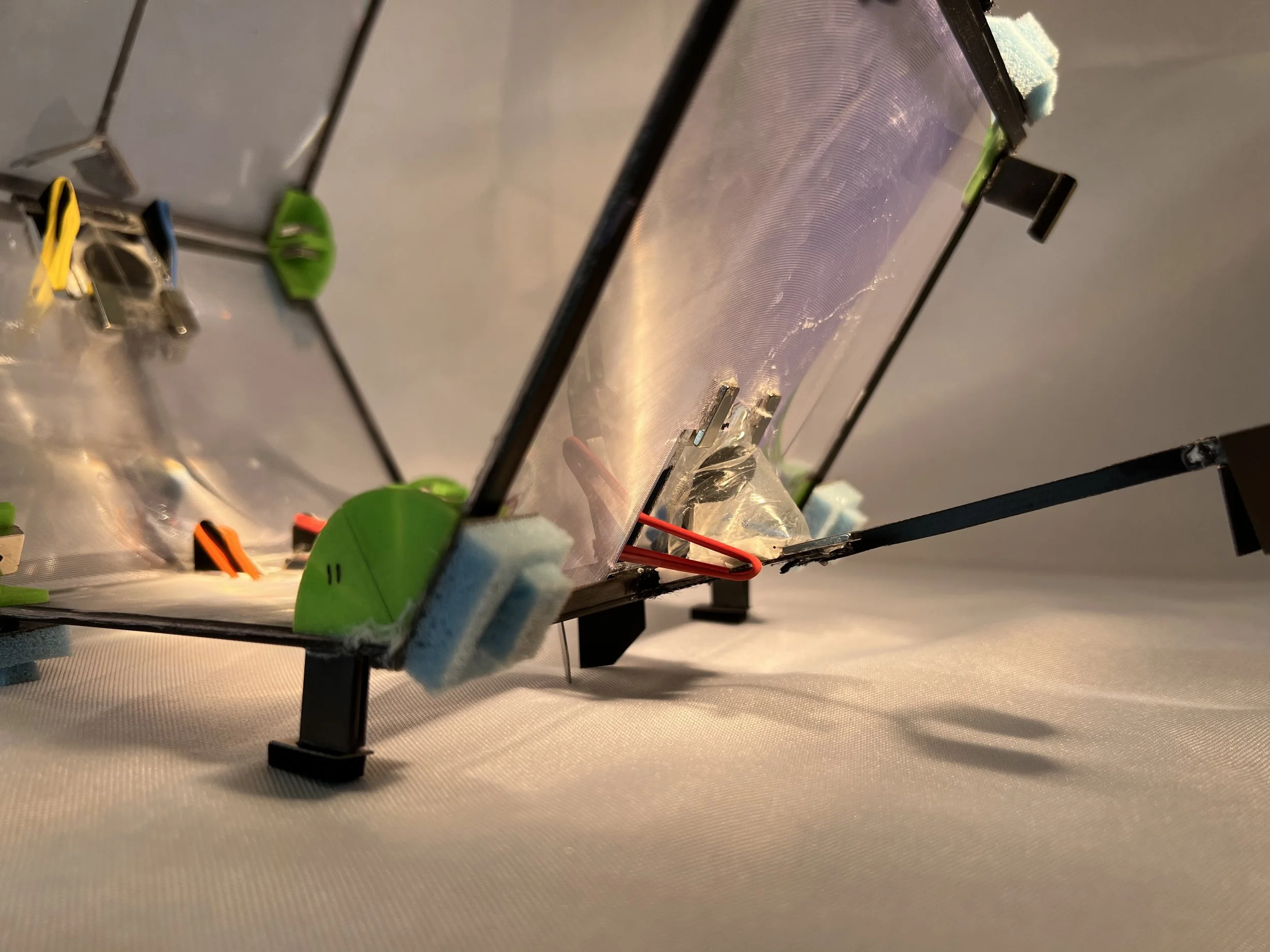
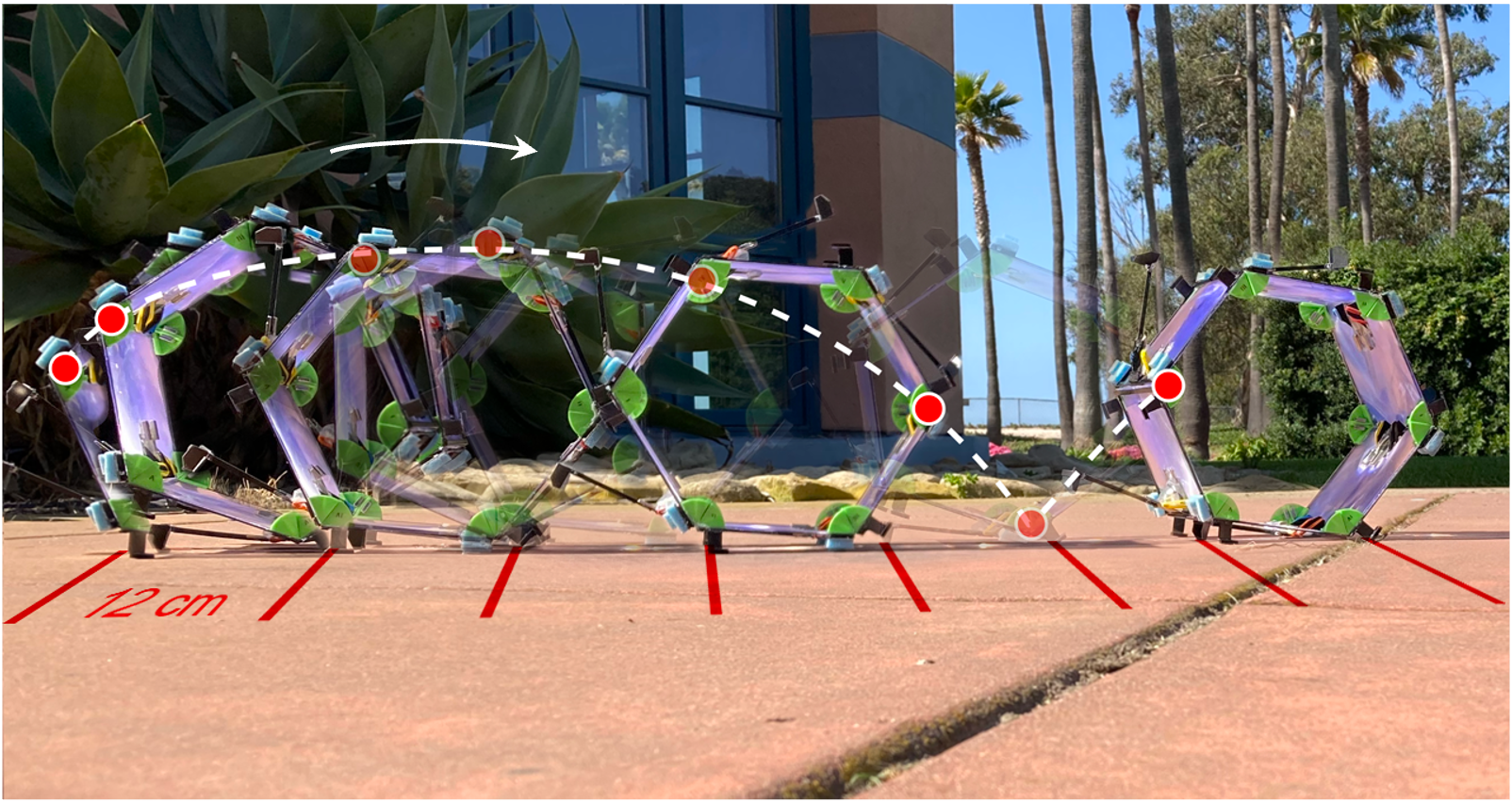
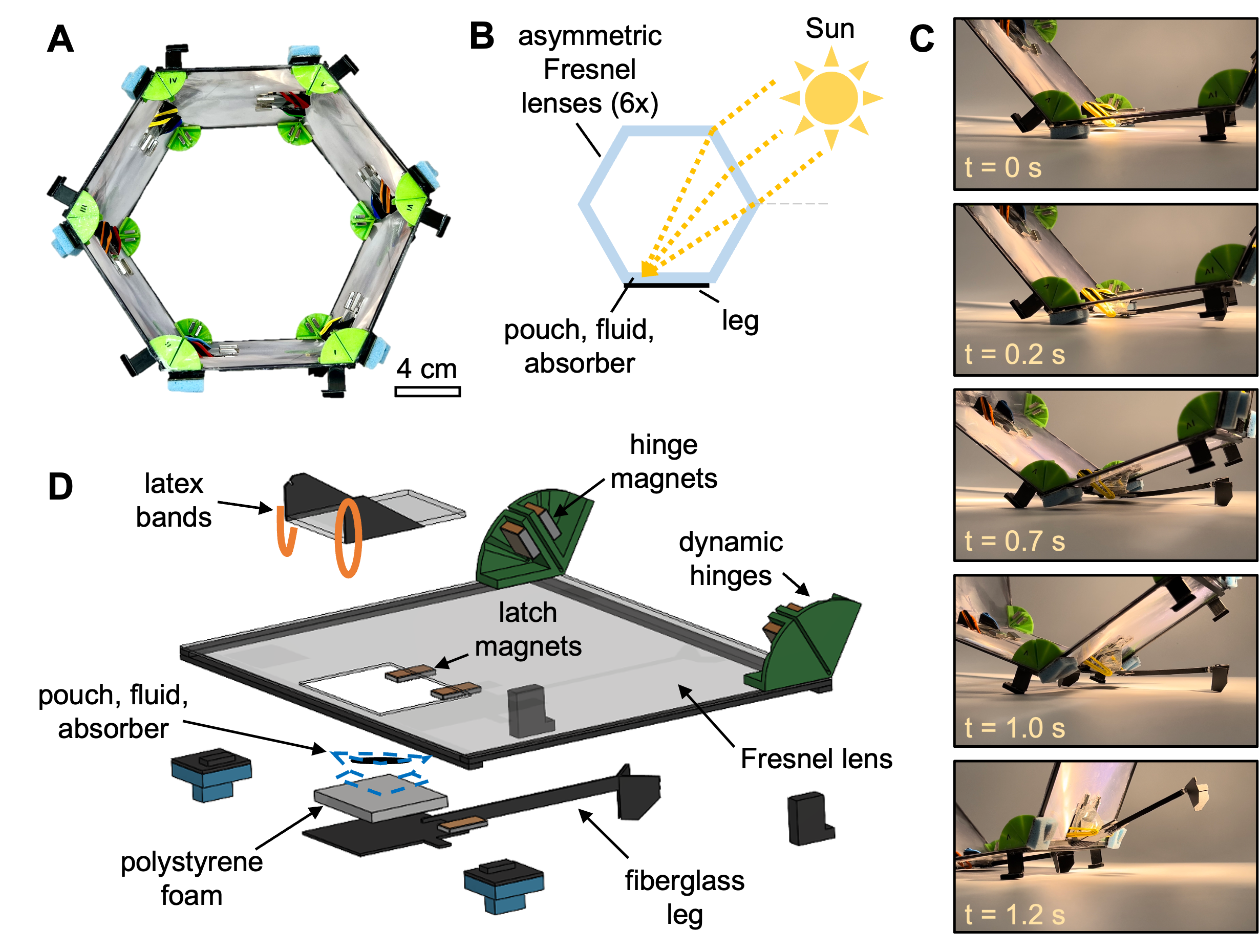


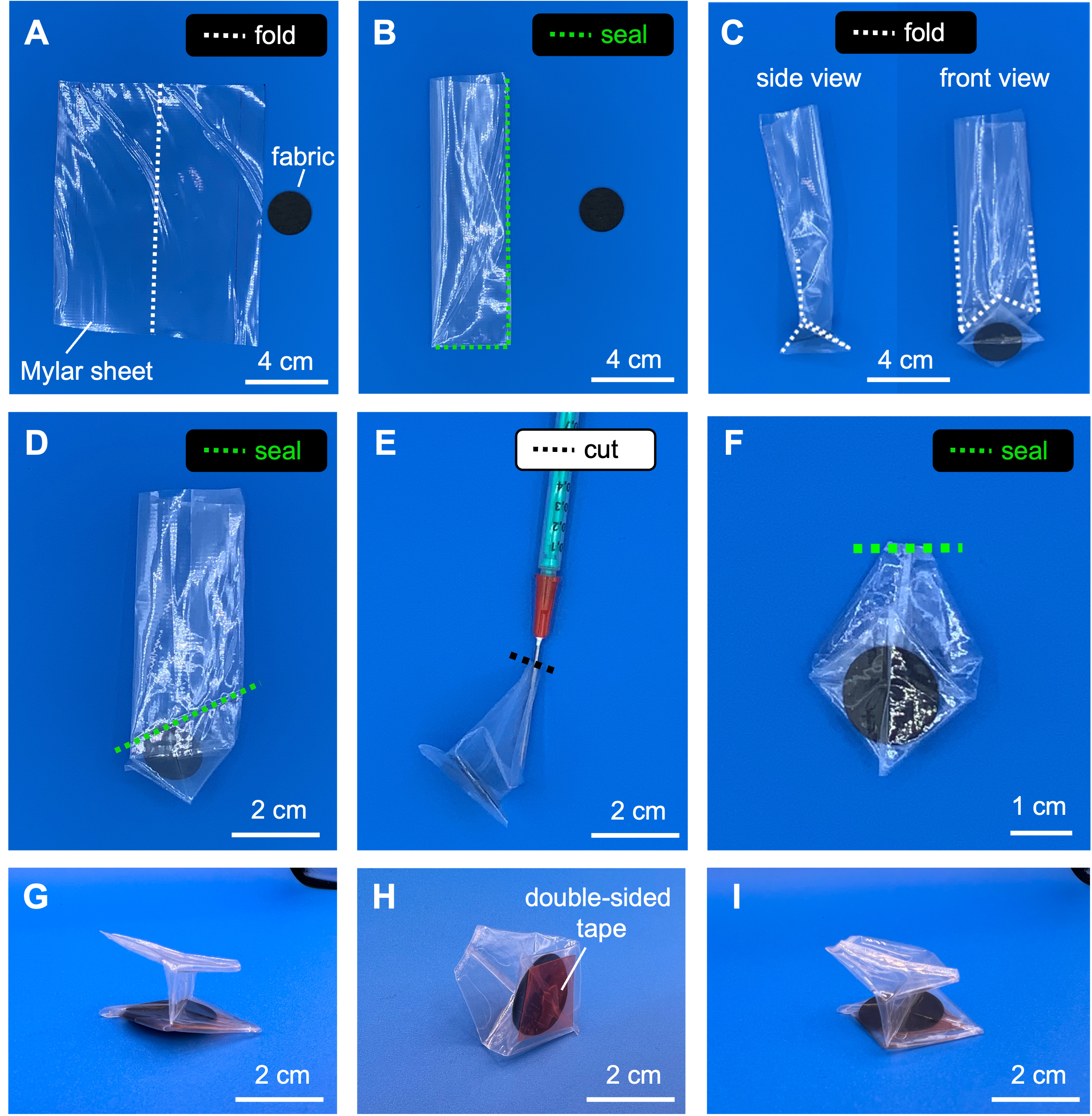
Bonus Content: Video of an early cardboard prototype designed to test the concept of latching as well as the thermodynamics. Watch to the end to hear the very satisfying “click” of the magnetic latch.